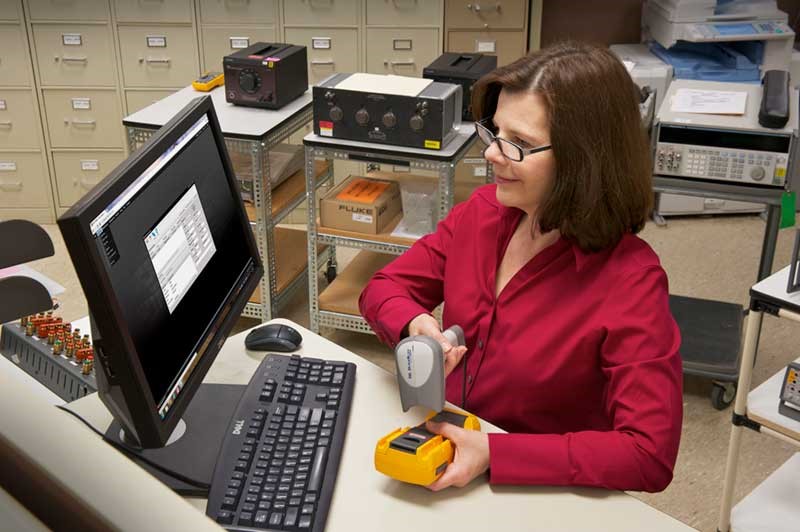
Os processos de fabricação requerem
centenas de dispositivos precisos para garantir as operações funcionando de
maneira confiável. Para manter esses dispositivos operando incessantemente e de
acordo com as especificações, eles exigem inspeções, reparos e calibrações
regulares. Seja o tempo, o fluxo, a temperatura ou a pressão que precisam ser
calibrados, esses equipamentos geralmente são enviados a um laboratório de
calibração ou um engenheiro de calibração é levado à fábrica para recalibrar o
ativo.
Existem vários motivos para calibrar um ativo,
que geralmente incluem a instalação de novos instrumentos, reparos ou modificações,
calibração programada, garantia de precisão e do bom funcionamento do
equipamento, estabilização após exposição a condições adversas, além de mudanças
ambientais, como o clima, por exemplo. Para minimizar o tempo de inatividade da
fábrica, confira abaixo cinco fatos que os engenheiros de automação e controle
precisam saber sobre calibração.
1. Manutenção preventiva para instrumentos
Pelas mesmas razões que os ativos elétricos
são verificados durante uma rota de manutenção preventiva, algumas áreas dos
ativos de instrumentação precisam ser verificadas porque podem fazer com que o
item pareça não estar calibrado. Às vezes, quando um produto parece estar um
pouco instável, é porque precisa ser limpo ou requer manutenção. Verifique os
ventiladores e filtros. Dependendo da máquina, eles precisam ser limpos mensal
ou trimestralmente.
Permitir que essas peças coletem sujeira e
poeira pode impedir que um ativo seja capaz de funcionar dentro de suas especificações
designadas. Então, por exemplo, uma peça ainda pode estar perfeitamente
calibrada, mas o ventilador não está resfriando o suficiente para funcionar com
desempenho máximo. Neste caso, os calibradores modulares de alta pressão Fluke
8370A garantem que uma ampla carga de trabalho de sensores de
pressão seja calibrada.
2. Siga o cronograma de calibração
As calibrações são geralmente certificadas
por um determinado período, mas a precisão do produto pode diminuir após essa
data. É importante seguir o cronograma que o laboratório de calibração
configura para cada produto.
Ao enviar o equipamento para um laboratório
de calibração, atente-se aos prazos. Os laboratórios de calibração ficam
ocupados e os tempos de envio podem ser imprevisíveis. A melhor maneira de
garantir que um produto seja calibrado e de volta à operação a tempo de evitar
atrasos na fábrica é enviá-lo com antecedência.
3. Forneça detalhes do instrumento, documentação
Ao enviar um produto para calibração ou trazer um engenheiro de calibração para a fábrica, forneça o máximo de informações sobre o equipamento. Se estiver sendo calibrado porque a precisão está diminuindo ou algo não está funcionando corretamente, informe o laboratório sobre os problemas presentes. Inclua informações sobre o desempenho e há quanto tempo o problema está presente. O contexto, além de como o produto é usado, pode ajudar a informar quais testes deverão ser realizados para garantir a precisão do produto.
Também pode ser útil informar o laboratório
sobre como os engenheiros de teste utilizam o equipamento. Nem todos os
aplicativos são usados conforme o esperado e o compartilhamento de
informações pertinentes com o laboratório de calibração garantirá melhores
serviços e o desempenho ideal do hardware de teste.
4. Conheça as incertezas do instrumento
Calibrações de produtos não garantem que tudo
esteja perfeito. Um laboratório de calibração possui requisitos específicos
para testar cada equipamento. Isso significa que a calibração é testada de
acordo com as especificações do fabricante e não em cada ponto de teste
possível.
Dependendo de como o produto for usado, a
calibração básica sugerida pelo fabricante pode não ser suficiente. Solicite um
ponto de calibração específico com base em como o produto é utilizado. Isso garante
que a calibração será precisa para as necessidades da aplicação.
Além disso, fornecer ao engenheiro de
calibração detalhes e um local de onde começar o teste ajudará a mitigar as
incertezas em torno dos testes para os quais a planta está usando um produto. O
multímetro Fluke
8558A de 8,5 dígitos oferece digitalização de alta resolução de 5 MS
por segundo para automação de sistemas em laboratórios e ambientes de teste de fabricação.
5. Verifique se há danos ao instrumento durante o transporte
Se o equipamento for enviado para calibração,
execute algumas verificações externas e alguns testes de medições quando ele
retornar para garantir que não foi danificado durante o transporte do laboratório
de calibração. Os pacotes podem cair ou serem manuseados de forma rude, o que
pode interferir na calibração. É importante garantir que tudo esteja
funcionando corretamente antes de usar o dispositivo na linha de produção
novamente.
Se um problema for observado ou se ele não
estiver calibrado corretamente, você terá a oportunidade de falar com o
laboratório antes que outros problemas sejam criados.
Quer saber mais? Clique aqui
e confira tudo sobre o universo da calibração.
Leia também:
3
maneiras de realizar inspeções térmicas
Verificação
da instalação elétrica: Por que fazer?